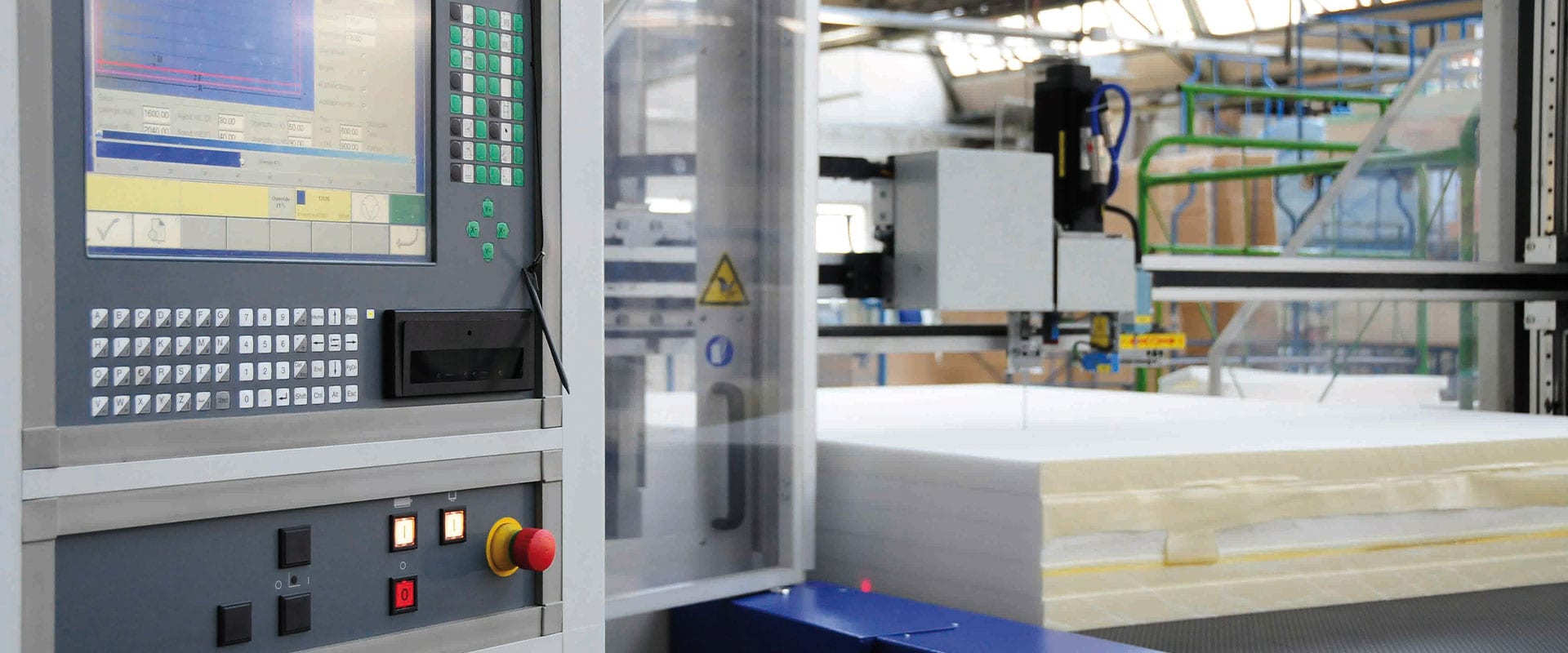
Good to know
Technische Informationen über unsere Schaumstoffe
Für ein umfassendes Verständnis und die bestmögliche Anwendung unserer Schaumstoffprodukte ist es entscheidend, technische Informationen bereitzustellen. Hier bieten wir Ihnen detaillierte Einblicke in die technischen Eigenschaften und Merkmale unserer hochwertigen Schaumstoffe. Wir möchten sicherstellen, dass Sie nicht nur über erstklassige Produkte verfügen, sondern auch über das Wissen, um diese effizient und effektiv in Ihren Anwendungen einzusetzen.
Historischer Überblick
1937: | Prof. Dr. Otto Bayer führt zum ersten Mal eine Polyaddition im Labor durch und entdeckt somit die Polyurethan-Chemie. |
1940: | Dr. A. Hoechtlen und Dr. W. Droste erzeugen im Labor den ersten Polyurethanschaum auf Polyesterbasis. |
1942/1945: | Der neue Polyurethanschaum wird von nun an im Bauwesen eingesetzt, um Hohlräume auszufüllen. |
1951: | Der erste Polyurethanschaum auf Polyätherbasis wird im Labor erzeugt. |
1952: | Es wird die erste Anlage zur kontinuierlichen Herstellung von Blockschaumstoffen gebaut, die Produktionsleistung liegt bei 20 kg/Minute. |
1955: | Es werden über 500.000 kg Schaumstoff auf Polyesterbasis erzeugt. Der Einsatz dieses neuen Materials für Kissen und Matratzen trifft den Geschmack der Erzeuger und der Kund:innen. |
1956: | Zum ersten Mal wird der weichelastische Polyurethanschaum auf Polyätherbasis industriell erzeugt. |
1968: | Die Produktionsleistung dieses aussergewöhnlichen Erzeugnisses der Polyurethan- Chemie erreicht über 200 Millionen kg/Jahr. |
1973: | Weltweit werden 1,2 Milliarden kg Polyurethanschaum erzeugt, wobei der Verbrauch in den Ländern Nordeuropas ca. 2kg/Kopf beträgt. |
1989: | Die Britische Regierung schreibt die Verwendung von Polyurethanschaumstoffen mit modifizierter Verbrennung (CM-HR) in der Wohnungseinrichtung vor. |
1991: | Beschluß zum Ausstieg des FCKW-Einsatzes bis zum Jahre 1995 |
Vom Erdöl zum PU-Schaum
Polyurethanschaum und seine Arten
Der Polyurethanschaum ist eine zellartige Struktur, die einen hohen Prozentsatz an Luft im Volumen einschließt. Es gibt zwei Hauptkategorien von Polyurethanschaum: harte und weichelastische Schaumstoffe. Während harte Schaumstoffe in Bereichen wie Bauwesen, Elektrotechnik und Verpackungsmaterialien Anwendung finden, konzentrieren wir uns in diesem Handbuch ausschließlich auf die Eigenschaften der weichelastischen Polyurethanschaumstoffe. Dieser elastische Polyurethanschaumstoff wird seit 1952 industriell hergestellt.
Die Rolle der Zusatzstoffe
Es ist wichtig zu beachten, dass die Herstellung von Polyurethanschaum neben den Grundrohstoffen auch viele andere Chemikalien erfordert, darunter Stabilisatoren, Emulgatoren, Katalysatoren, Farbstoffe usw. Diese Zusatzstoffe sind entscheidend, um verschiedene Eigenschaften wie spezifisches Gewicht, Weichheit, Beständigkeit, Dehnungsfestigkeit und Elastizität zu erreichen. Sie tragen wesentlich zur Qualität des Endprodukts bei.
Präzision in der Dosierung
Die einzelnen Bestandteile werden mithilfe eines Druckpumpensystems direkt aus den Tanks entnommen. Die Genauigkeit der Dosierung in dieser Phase ist von größter Bedeutung, um ein gleichmäßiges Produkt zu gewährleisten. In modernen Anlagen werden die Durchflussmengen jeder Komponente sorgfältig überwacht und kontinuierlich aufgezeichnet.
Kurz nachdem die Komponenten miteinander in Kontakt kommen, werden sie gleichmäßig auf eine Spezialpapierbahn aufgetragen, und die Mischung bewegt sich auf einem Förderband. Die anfänglich 0,5 bis 1,5 cm dicke Flüssigkeitsschicht wächst zu einem über 1 m hohen Block heran. Das Gas, das zur Expansion des Schaumstoffs benötigt wird, entwickelt sich hauptsächlich während der Polymerisation des Schaums. Diese exotherme Reaktion erzeugt Wärme. Die Polymerisation ist bereits wenige Meter nach dem Verlassen des Mischkopfs abgeschlossen.
Synergisch-physikalische Faktoren
Die Herstellung von PUR-Schaumstoff erfolgt nicht nur durch chemische Prozesse, sondern auch durch physikalische Vorgänge. Daher müssen verschiedene synergisch-physikalische Faktoren berücksichtigt werden, darunter die Temperatursteuerung der Rohstoffe, freigesetzte und in den Rohstoffen dispergierte Gase, Luftdruck, Luftfeuchtigkeit und Raumtemperatur. Diese Faktoren sind entscheidend für die Qualität des Endprodukts.
Die Struktur des Polyurethanschaums
Die Bienenwabenstruktur und die dünnen Wände der Schaumzellen sind ausschlaggebend für die Weichheit, Elastizität und Beständigkeit dieses Materials. Zudem ist Polyurethanschaum leicht, luft- und feuchtigkeitsdurchlässig, was ihn zu einem idealen Polstermaterial macht.
Lagerung und Weiterverarbeitung
Die Blockschaumlänge besteht vorwiegend aus 60 Meter langen Blöcken, die automatisch von einem computergesteuerten System gelagert werden. Die Weiterverarbeitung der PUR-Schaumblöcke erfolgt üblicherweise 72 Stunden nach der Herstellung, da der Schaum erst nach 24 Stunden stabil wird.
Eigenschaften von PU-Schaum
Allgemeines
Die Blockschaumstoffe werden in zwei Hauptgruppen unterteilt: Polyurethanschaum auf Polyätherbasis und auf Polyesterbasis.
Physikalische Eigenschaften
Die Schaumstoffe auf Polyätherbasis unterscheiden sich von denen auf Polyesterbasis in folgenden Einzelheiten:
- Polyätherschaumstoffe sind hochelastisch, während weniger elastische Polyesterschaumstoffe einen höheren Stossabsorptionsgrad aufweisen.
- Polyesterschaumstoffe sind gegenüber organischen Lösungsmitteln beständiger.
- Polyätherschaumstoffe sind hydrolysebeständig.
- Beide Schaumstoffe bieten exzellente thermische Isolationseigenschaften.
- Die Wärmeleitzahl des weichen Polyurethanschaums beträgt etwa 0,04 Kcal/h.
- Zusätzlich weisen beide gute Schallabsorptionswerte bei mittleren und hohen Frequenzen auf.
Die hs-Schaumstoff verarbeitet Schaumstoffe in verschiedenen Härtegraden und Raumgewichtsklassen (Standard von 16–80 kg/m³ – Kaltschaum von 21–65 kg/m³). Die Feuchtigkeitsaufnahme beträgt ca. 2 % bei 90 % relativer Luftfeuchtigkeit. Diese Feuchtigkeitsaufnahme kann während der Herstellung variieren. Bei dynamischer und statischer Beanspruchung erweicht sowohl Polyäther- als auch Polyesterschaum, wobei Polyesterschaum stärker verformt, aber weniger reißt. Unter optimalen Produktionsbedingungen gilt die Regel: Je höher das Raumgewicht, desto geringer ist die Verformung.
Beständigkeit gegenüber Chemikalien
Eine Tabelle zeigt das Verhalten von PUR-Schaum gegenüber verschiedenen Chemikalien. PUR-Schaum auf Polyätherbasis zeigt eine relative Beständigkeit gegenüber Säuren und Alkalien. Polyestertypen hingegen sind gegenüber allen organischen Lösungsmitteln widerstandsfähiger.
Hydrolyse-Alterung
Unter Hydrolyse versteht man die Aufspaltung von Molekülen bei Kontakt mit Wasser. Die in der Luft enthaltene Feuchtigkeit kann zur Hydrolyse führen. Im Vergleich zu Polyätherbasierten Schaumstoffen zeigen Polyesterschaumstoffe eine geringere Hydrolysebeständigkeit.
Oxidationsalterung
Polyurethanschaumstoffe, sowohl auf Polyester- als auch auf Polyätherbasis, sind gegenüber Sauerstoff sehr widerstandsfähig.
Lichtalterung
Polyurethanschaum kann durch Lichteinwirkung (Tages- und Kunstlicht) vergilben. Diese Verfärbung ist auf die Oxidation bestimmter Molekülgruppen im Schaum zurückzuführen. Bei Polyesterschaum ist die Lichtvergilbung geringer als bei Polyätherschaum. Je schwerer der Schaumstoff, desto geringer ist die Verfärbung, die jedoch die physikalisch-mechanischen Eigenschaften nicht beeinflusst.
Physiologische Eigenschaften
Polyurethanschaum verursacht bei Hautkontakt keine Hautreizungen oder Dermatosen. Experimente haben gezeigt, dass die Einnahme von Schaumstoff keine Schädigungen verursacht.
Beständigkeit gegenüber Mikroben
Beobachtungen haben ergeben, dass Schimmelpilze und Bakterien bei extrem hoher Luftfeuchtigkeit den Polyurethanschaum schädigen können. Um dies zu verhindern, kann der Schaumstoff mit antimikrobiellen Stoffen wie Sanitized® behandelt werden.
Temperaturbeständigkeit
Polyurethanschaum kann auch bei Temperaturen bis zu 100 °C ohne wesentliche Reduktion der physikalischen Eigenschaften eingesetzt werden. Ein Waschvorgang bei 90 °C führt zu thermischer, mechanischer und chemischer Beanspruchung des Materials, wobei Qualitätsware diesen Belastungen ziemlich gut standhält und sich nur begrenzt verformt. Die Zersetzungstemperatur liegt bei > 180 °C, und die Entzündungstemperatur bei > 400 °C.
Gasentwicklung bei Verbrennung von Polyurethanschaum
Wie bei anderen Naturstoffen (Holz, Wolle, Leder) werden bei der Verbrennung von Polyurethanschaum Kohlenmonoxid, Stickoxide und Kohlendioxid freigesetzt. Der Prozentsatz der bei der Verbrennung von Schaumstoffen entweichenden Gase ist jedoch nicht höher als bei der Verbrennung der oben genannten Naturstoffe.
Chlorfluorcarbone (FCKW)
Alle bei hs-Schaumstoff verwendeten Schaumstofftypen kommen gänzlich ohne den Einsatz von Chlorfluorcarbonen (FCKW) aus, was einen wichtigen Beitrag zum Schutz der Umwelt darstellt.
Entflammbarkeit von Polyurethanschaum
Polyurethanschaum ist, wie die meisten organischen Stoffe, brennbar. Durch den Einsatz von Additiven und besonders modifizierten Rohstoffen bei der Schaumherstellung ist es jedoch möglich, die Entflammbarkeit zu reduzieren. Wir verfügen über diverse Schaumstoffe, die den strengsten internationalen Anforderungen in Bezug auf Brandschutz entsprechen.
Lagerung von PU-Schäumen
Unter neutralen Lagerbedingungen ist Polyurethan-(PUR-)Weichschaum über einen langen Zeitraum lagerfähig. Da die Lagerbedingungen bei den Kund:innen der Polyurethan-Weichschaumhersteller im Einzelnen nicht bekannt sind und hierauf auch kein Einfluss genommen werden kann, ist grundsätzlich keine Aussage über eine Mindesthaltbarkeitsdauer möglich. Um die zugesicherten Eigenschaften von PUR-Weichschaum im Anlieferungszustand möglichst unverändert zu erhalten, sollten die folgenden Lagerhinweise beachtet werden:
- Lagerung in gut durchlüfteten Räumen
- Schutz vor UV-Einstrahlung
- Schutz vor Nässe und Feuchtigkeit, auch hohe Luftfeuchtigkeit
- Schutz vor flüchtigen Bestandteilen, wie z.B. niedermolekularen Weichmachern, da diese vom PUR-Weichschaum aufgenommen werden können, was zu einer deutlichen Verschlechterung der Fogging-Werte führen kann.
Hinsichtlich der sicherheitstechnischen Einstufung in Bezug auf das Brandrisiko sind Polyurethan-Weichschäume in die Brandgefahrenklasse 4.4 eingestuft (siehe VdS Nr. 2292 6/87, Richtlinie für Sprinkleranlagen, Planung und Einbau, Anhang A2). Der Lagerhalter sollte sicherstellen, dass intern festgelegte oder mit Zulieferern vereinbarte maximale Lagerreichweiten beachtet werden und grundsätzlich das FIFO-Prinzip (First-In-First-Out) anwenden.
Stoffe, die nicht in PU-Schäumen enthalten sind
Gemäß den europäischen Richtlinien 76/769/CEE – 2002/95/CE und 2003/11/CE, die sich auf verbotene gefährliche Stoffe beziehen, bestätigen wir, dass unsere Polyurethan-Schäume die folgenden verbotenen Substanzen nicht enthalten:
- Aliphatic CHC
- 1.1.1.-Trichloroethane Tetrachloromathane
- Asbestos
- Lead and Lead compounds
- Cadmium and Cadmium Compounds
- Chlorinated dioxins and furans Brominated dioxins and furans
- CFC and Halons
- FC – HCFC – HBrFc – Methyl bromide
- Formaldehyde
- Halogenated biphenyls, terphenyls and naphthalenes
- Halogenated aromatic compounds
- Pentachlorophenol (PCP) – Pentachlorophelol sodium salt – Other PCP salts and Compounds
- Polychlorinated biphenyls (PCB) – Polychlorinated terphenyls (PCT) –
- Monomethyltetrachloro diphenylmethane – Monomethyldichlorodiphenylmethane –
- Monomethydibromodiphenilmethane
- Mercury and Mercury compounds
- Polybromurated Biphenyls (PBB) – Polybromurated Diphenylethers (PBDE)
- Pentabromodiphenylether (PBDE) – and Octabromodiphenylether (octaPBDE)
- Heavy metals (Pb, Cd, Cr VI, Hg)
- Tar Oils
- Carcinogenic mutagenic and reproduction toxic chemicals
- Chromium (VI) compounds
- Poly-brominated biphenyls and poly-brominated diphenylethers
- Antimony trioxide
- Arsenic and Arsenic compounds
- Azo compounds with carcinogenic amino compounds
- Beryllium and beryllium compounds
- N, N, – dimethlyformamide (DMF)
- Synthetic mineral fibres classified as carcinogenic
- Radioactive substances
- Selenium and Selenium compounds
- Brominated flame-retardants
- Chlorinated paraffins
Prüfmethoden
Charakteristik eines Schaumstoffes
Um die Charakteristik eines Schaumstoffes zu bestimmen, werden folgende physikalische Werte gemessen:
Raumgewicht
Das Raumgewicht zeigt das Gewicht des Schaumstoffes pro Volumeneinheit in kg/m³ an. Ein Musterblock, von dem eine Haut entfernt wurde, wird senkrecht zur Zuwachsachse in Schichten geschnitten: der Durchschnitt der einzelnen Gewichtswerte gibt das Raumgewicht des Blockes an. Die Methoden zur Bestimmung des Raumgewichtes sind: UNI 6349, DIN 53420, ISO 1855. Toleranz +/- 5 %.
Eindruckhärte
Die Eindruckhärte oder der Stauchwiderstand ist die Kraft, die notwendig ist, um einen Eindringkörper (dessen Form und Abmessung festgelegt wurden) in das Prüfmaterial bis zu 25 %, 40 % und 65 % seiner eigenen Dicke hineinzudrücken. Die Probe, die größer als der Eindringkörper ist, wird in die Mitte der Dynamoeterplatte gelegt. Bei jeder Kompression des Prüfmaterials bis zu 25 %, 40 % und 65 % der eigenen Dicke wird die Belastung 30 Sekunden lang gehalten; dann wird der Wert des Stauchwiderstandes in Newton=N bestimmt.
Die Ergebnisse werden als Eindruckhärte oder Stauchwiderstand bei 25 %, 40 % und 65 % Belastung in Newton ausgedrückt. Der Stauchungsfaktor oder Sagfaktor ist das Verhältnis zwischen dem Widerstand bei 65 % und bei 25 % Stauchung und stellt eine gültige Angabe zur Bewertung der Eignung und des Komforts des Schaumstoffes dar. Je höher der Wert ist, desto größer ist der Komfort. Die konventionellen Polyätherschaumstoffe haben Werte von a/b=1,9, während die hs-Kaltschäume Werte von a/b=2,9 aufweisen.
Stauchhärte
Die Stauchhärte oder der Kompressionswiderstand ist der Druck (in Kilopascal=Kpa ausgedrückt), der notwendig ist, um einen Probekörper bis zu 40 % seiner ursprünglichen Dicke mittels eines Eindringkörpers (dessen Form und Abmessung festgelegt wurden) zusammenzudrücken. Der Probekörper ist ein Parallelepiped mit den Abmessungen 100 x 100 x 50 mm; man kontrolliert die Abmessung des Probekörpers und bestimmt die zu komprimierende Fläche; man legt denselben in die Mitte der Platte des Messgerätes, drückt ihn um 40 % seiner eigenen Dicke zusammen und bestimmt die dazu notwendige Kraft. Das Ergebnis wird in Kpa ausgedrückt. Die Methoden zur Bestimmung der Stauchhärte sind: DIN 53577, UNI 6351, ISO 3386. Toleranz +/- 15 %.
Zugfestigkeit
Der Zugwiderstand wird in Kpa oder kg/cm² ausgedrückt und ist das Verhältnis zwischen der höchsten Kraft, die notwendig ist, und seiner Querschnittfläche. Die Bruchdehnung ist die in Prozenten ausgedrückte Differenz zwischen der Ursprungslänge und der im Augenblick des Bruches gemessenen Länge. Der Probekörper muss aus Platten mit 10–15 mm Dicke gestanzt werden. Dann wird er in die Backen des Dynamometers gespannt und einer konstanten Zugkraft ausgesetzt. Im Augenblick des Bruches wird die höchste Kraft und die erreichte Länge gemessen; sodann wird die Zugfestigkeit (kpa) und die Bruchdehnung (%) berechnet. Die Methode zur Bestimmung der Zugfestigkeit ist: DIN 53571.
Druckverformungsrest
Der Druckverformungsrest ist der Wert des prozentuellen Dickeverlustes des Probekörpers nach der Kompression unter besonderen Bedingungen. Der Probekörper ist ein Parallelepiped mit quadratischer Basis und einer Dicke von 50 mm. Dieser wird zwischen zwei parallele Platten gespannt und bis zu 50 %, 75 % und 90 % seiner ursprünglichen Dicke zusammengedrückt. Anschließend wird er für 22 Stunden in einem Luftumlaufofen bei einer Temperatur von 70 °C aufbewahrt. Nach dieser Zeit wird er ausgespannt und muss 30 Minuten ruhen, bevor seine Dicke gemessen wird. Die Ergebnisse werden als Dickeverlust – bezogen auf die verschiedenen Kompressionswerte – in Prozenten ausgedrückt. Die Methode zur Bestimmung des Druckverformungsrestes ist: DIN 53572, UNI 6352.
Dauerschwingversuch
Der Dauerschwingversuch ist der in Prozent ausgedrückte Verlust der Dicke und des Druckwiderstandes, den ein Probekörper aufweist, nachdem er bei einer Frequenz von 60 Pulsationen pro Minute 75.000 Mal bis zu 75 % seiner ursprünglichen Dicke zusammengedrückt wurde. Zuerst wird der Kompressionswiderstand und die Ursprungsdicke des Probekörpers bestimmt. Dann wird er 75.000 Mal bei einer Frequenz von 60 Pulsationen pro Minute zusammengedrückt. Nach einer Ruhezeit von ca. 30 Minuten werden die Dicke und die Stauchhärte erneut gemessen. Die Ergebnisse werden als Verlust der Stauchhärte in Prozenten ausgedrückt. Die Methode zur Bestimmung des Dauerschwingversuchs ist: UNI 6356.
Elastizität
Die Elastizität ist das prozentuale Verhältnis zwischen der Rückprallhöhe und der Ausgangshöhe einer Kugel (mit vorherbestimmten Abmessungen und Gewicht), die freifallend aus einer bestimmten Höhe senkrecht auf die Oberfläche des Probekörpers trifft und zurückprallt. Die Methode zur Bestimmung der Elastizität ist: UNI 6357.
Luftdurchlässigkeit
Die Elastizität und die Härte eines Schaumstoffes sind auch von der Größe und der Öffnung der Schaumzellen abhängig. Bei gleichbleibenden anderen Werten sind Schaumstoffe mit größeren und offenen, d.h. kommunizierenden Zellen elastischer. Mit einem besonderen Gerät wird die Durchfluss-Schwierigkeit (Energiegefälle) eines Luftstroms durch ein Schaumstoffmuster gemessen. Bei kleinen und geschlossenen Zellen misst man hohe Energiegefälle, d.h. niedrige Luftdurchlässigkeit. Bei großen und offenen Zellen hat man niedrige Energiegefälle und hohe Luftdurchlässigkeit.
Brandmethoden
MVSS 302:
Im Jahr 1972 wurden in den USA konkrete Anforderungen an das Brandverhalten von Werkstoffen und Teilen im Innenraum von Personenkraftwagen, Lastwagen und Omnibussen unter dem Namen MVSS 302 erlassen. Dabei werden folgende Prüfparameter verwendet:
- Probekörper: Fünf Proben mit Abmessungen von 356 x 100 x Anwendungsdicke (maximal 12,7 mm) und Messmarken bei 38 mm, 76 mm, 292 mm. Die Messstrecke beträgt 254 mm.
- Probeanordnung: Horizontal.
- Zündquelle: Ein Bunsenbrenner mit 9 mm Durchmesser und einer Flammhöhe von 38 mm wird 15 Sekunden lang angezündet.
- Beurteilung: Die Flammausbreitungsgeschwindigkeit über die Messstrecke darf maximal 4 inch/min (101,6 mm/min) betragen.
In Deutschland beträgt die höchstzulässige Flammausbreitungsgeschwindigkeit für prüfpflichtige Innenraumteile gemäß § 30 StVZO 110 mm/min. Die MVSS 302 wurde von deutschen Kfz-Herstellern mehrfach modifiziert, darunter die OPEL-Norm 261 (max. Brennrate 75 mm/min) und TL-VW 1010 (Messmarken 38, 88, 292 mm).
BS 5852 PART 2 CRIB 5 FÜR CMHR+CM-SCHAUMSTOFFE:
Im Jahr 1980 erließ das britische Parlament Sicherheitsverordnungen für Polstermöbel, gefolgt von den Prüfmethoden BS 5852/1/2 bis 1982. Diese Verordnungen erforderten, dass alle zum Verkauf stehenden Polstermöbel mit einem Etikett versehen werden, das Kunden über das Brandrisiko des Möbelstücks informiert.
Polsterkombinationen wurden auf ihr Brandverhalten untersucht, wobei verschiedene Zündquellen wie Zigaretten, Gasflammen und genormte Körper aus Holzstäbchen verwendet wurden. Als Reaktion auf öffentlichen Druck verbot das britische Parlament im Mai 1988 konventionelle PU-Schaumstoffe ab dem 01.03.1989 als Möbel- und Matratzenfüllung. Ein Verbot für brennbare Bezugsmaterialien wurde ebenfalls erlassen.
Um den PU-Schaum-Herstellern eine praktikable Prüfmethode zu bieten, wurde der CMHR (Combustion Modified High Resilient) Schaum entwickelt. Ein charakteristischer Test für diesen Schaumtyp beinhaltet Folgendes:
Auf einem genormten Metallgestell werden zwei Schaumstoffkissen (Sitzteil: 300 x 450 x 75 mm; Rückenteil: 450 x 450 x 75 mm) rechtwinklig zueinander angeordnet. Die Kissen sind mit flammwidrigem Polyesterfaserstoff bezogen. Auf das „Sitzteil“ wird ein kaminförmiges Gebilde aus 20 Holzstäbchen gelegt und mit Propanol entzündet.
Anforderungen:
- Flammen müssen spätestens nach 10 Minuten erloschen sein.
- Glimmen und Rauchentwicklung müssen spätestens 60 Minuten nach Zündung enden.
- Der Gewichtsverlust des gesamten Modells darf nach Beendigung des Versuchs nicht mehr als 60 g betragen.
Diese Prüfung bewertet die Eignung des PU-Schaumstoffs als Polsterfüllung. Die Materialkombination in einem Möbelstück unterliegt einer weiteren Bewertung nach Auswertung des Brandverhaltens bei verschiedenen Zündquellen, jedoch gibt es in Deutschland bisher keine vergleichbaren Anforderungen.
CALIFORNIA-TEST T.I.B 117:
Das „Flammability package“ des US-State of California Department of Consumer Affairs – Bureau of Home Furnishings – von 1980 legte Regeln für die Entflammbarkeit von Matratzen, Polstermöbeln und den verwendeten Vormaterialien fest. Dies beinhaltete das „Technical Information Bulletin 177 Section A Part 1“, kurz TIB 117, das Prüfmethoden und Anforderungen an das Brandverhalten geeigneter Schaumstoffe beschreibt:
- Probekörper: 10 Proben mit Abmessungen von 305 x 76 x 12,7 mm, wobei 5 Proben 24 Stunden bei 104 °C gealtert werden.
- Probeanordnung: Die Proben hängen vertikal im Testrahmen, wobei das untere Ende 20 mm über dem Brennrohrende liegt.
- Zündquelle: Ein Bunsenbrenner mit 10 mm Durchmesser und einer Flammhöhe von 40 mm wird 12 Sekunden lang verwendet.
- Anforderungen:
- Die durchschnittliche Länge der verkohlten Zone aller Proben darf maximal 152 mm betragen, wobei eine Probe bis zu 203 mm erreichen darf.
- Die durchschnittliche Nachbrennzeit, einschließlich abgetropfter Teile, aller Proben darf maximal 5 Sekunden betragen, wobei eine Probe bis zu 10 Sekunden erreichen darf.
- Die durchschnittliche Nachglimmzeit, einschließlich abgetropfter Teile, darf maximal 15 Sekunden betragen.
Diese Prüfung ähnelt weitgehend der FAR Part 25b für die Innenausstattung von Flugzeugen und entspricht den Anforderungen in DIN 4102 B2 (Deutschland) und SIA 183/2 Brandklasse (Schweiz).
DIN 4102 / DIN EN 1350-1 BZW. 13501-1:
Diese deutsche Norm wird hauptsächlich zur Beurteilung des Brandverhaltens von Baustoffen verwendet und unterteilt Materialien in nicht brennbare (Klasse A1 und A2) und brennbare (B1, B2, B3). Schaumstoffe fallen fast immer in die Klasse B3 („leicht entflammbar“) nach DIN 4102. Die Klasse B2 („normal entflammbar“) erfordert, dass die Flamme nach Entfernen der Zündquelle innerhalb von 20 Sekunden nicht eine Markierungslinie 190 mm über der Probe erreicht. Die Klasse B1 („schwer entflammbar“) erfordert den Bestehen eines Brandschachttests.
EN 1021 – 1/2 : 1994 FÜR DIN 66084/DIN54341:
Diese EU-weite Norm bewertet die Reaktion von Materialien auf eine brennende Zigarette und eine Butanflamme (ein simuliertes Streichholz). Sie ersetzt nationale Tests wie DIN 54342 – 1/2 in Deutschland und BS 5852: 1990 in Großbritannien.
- EN 1021 – Teil 1 (Klassifizierung nach DIN 66084 P-c): Eine brennende Zigarette wird in den Testmodellwinkel gelegt und der Stoff darf nach 60 Minuten nicht brennen oder glimmen.
- EN 1021 – Teil 2 (Klassifizierung nach DIN 66084 P-b): Eine Butanflamme, die ein Streichholz simuliert, wird in den Winkel gelegt und der Stoff darf nach Entfernen der Flamme innerhalb von 2 Minuten nicht brennen.
DIN 54341 (Klassifizierung nach DIN 66084 P-a):
Diese Klasse umfasst Polsterverbunde, die die Anforderungen von DIN 54341 bei jeder Einzelprüfung erfüllen müssen. Hierbei wird ein Papierkissen mit 100 g Gewicht auf den Prüfkörper gelegt. Die Flammen müssen innerhalb von 15 Minuten erlöschen, wobei die Flammhöhe und die Seitenränder bestimmten Anforderungen entsprechen müssen.
FAR 25.853 (B):
Die FAR 25.853 (B) ist eine amerikanische Testmethode, die in der Flugzeugindustrie Anwendung findet. Dabei wird das Entzündungsverhalten, die Flammenausbreitung und das Abtropfverhalten von Materialien gemessen. Der Test erfolgt bei einer Beflammungsdauer von 12 Sekunden (Klassifikation a) und 60 Sekunden (Klassifikation b).
DIN 75200 (+ISO 3795):
Die DIN 75200 ist eine deutsche Norm, die die Brenngeschwindigkeit von Materialien im Insassenraum von Kraftfahrzeugen bewertet. Ein horizontal angeordneter Probekörper (138 x 80 mm) wird in einem U-förmigen Halterahmen über 15 Sekunden einem Brenner mit mäßiger Flammbeanspruchung ausgesetzt. Es wird festgestellt, wann die Flamme erlischt oder die Flammenfront eine bestimmte Brennstrecke zwischen zwei Meßmarken durchläuft. Die internationale Norm ISO 3795 basiert im Wesentlichen auf der DIN 75200.
ASTM D 1692-68:
Ursprünglich für die Bauindustrie in den USA entwickelt, wird die ASTM D 1692-68 Testmethode nun auch in der Automobil- und Transportindustrie zur Bewertung des Brandverhaltens von Materialien verwendet. Ein horizontal auf einem Drahtgeflecht liegender Probekörper (15 x 5 x 1,27 cm) wird an einem Ende entzündet. Nach Entfernen der Zündquelle (Bunsenbrenner) werden Zeit und Brennstrecke bis zum Erlöschen der Flamme gemessen. Erreicht die Flamme vor Erreichen der Messmarke bei 12,5 cm das Erlöschen, erhält der Schaum die Klassifizierung „selbsterlöschend nach ASTM D 1692-68“.
UL 94 HF 1:
Die Underwriters Laboratories Inc. (UL) führt sicherheitstechnische Prüfungen für den Schutz von Menschen und Sachwerten durch. Die UL 94 ist eine Vorschrift zur feuersicherheitlichen Prüfung von Kunststoffen, insbesondere Schaumstoffen. Die Stufe HF 1 stellt hohe Anforderungen an die Materialien:
- Probekörper: Es werden 2 x 5 Proben mit Abmessungen von 152 x 50,8 x 12,7 mm verwendet, wobei 5 Proben 168 Stunden bei 70 °C gelagert werden.
- Probeanordnung: Die Probe liegt horizontal auf einem Drahtnetz mit definierter Maschenweite, darunter eine horizontale Wattelage 305 mm unterhalb der Probe.
- Zündquelle: Ein Bunsenbrenner mit aufgesetzter Düse erzeugt eine 47 mm breite Flamme, wobei die Höhe der nicht leuchtenden Flamme 38 mm beträgt.
- Beflammungsdauer: 60 Sekunden
Ergebnisse:
- Kein Nachbrennen länger als 2 Sekunden nach Beflammungsende bei mindestens 4 von 5 Proben.
- Bei keiner Probe Nachbrennen länger als 10 Sekunden nach Beflammungsende.
- Keine Zerstörung einer Probe über die 57 mm-Marke hinaus.
- Kein Nachglühen einer Probe länger als 30 Sekunden nach Beflammungsende oder über die 57 mm-Marke hinaus.
- Kein brennendes Abtropfen.
EG 95/28
Die EG 95/28 ist eine Richtlinie der Europäischen Union, die das Brennverhalten von Werkstoffen in der Innenausstattung bestimmter Kraftfahrzeugklassen regelt. Ziel ist die Angleichung der Rechtsvorschriften der Mitgliedstaaten in Bezug auf diese Materie. Die Richtlinie betrifft insbesondere Kraftomnibusse der Klasse M3, die zur Beförderung von mehr als 22 Fahrgästen bestimmt sind, wobei Fahrzeuge für stehende Fahrgäste oder den Stadtverkehr ausgenommen sind. Die Mitgliedstaaten dürfen Fahrzeuge oder Bauteile, die den in dieser Richtlinie festgelegten Bedingungen entsprechen, weder verweigern noch verbieten.
BKZ (SCHWEIZER BRANDKENNZIFFER)
Die Brennbarkeit von Baustoffen wird anhand der Brandkennziffer (BKZ) in die Klassen 3–6 eingeteilt, wobei Zündbarkeit und Abbrandgeschwindigkeit maßgebliche Faktoren sind. Baustoffe der Brennbarkeitsgrade 1 und 2 sind nicht als Baustoffe zugelassen. Die Qualmbildung wird durch Messung der Lichtabsorption beim Abbrand eines Prüfkörpers ermittelt und in die Qualmgrade 1–3 eingeteilt, wobei diese das Qualmverhalten beschreiben. Die Brandkennziffer setzt sich aus dem Brennbarkeitsgrad und dem Qualmgrad zusammen und dient zur Klassifizierung von Baustoffen.
Verarbeitungsmethoden
- Horizontal schneiden
- Vertikal schneiden
- Horizontal Kontur schneiden
- Vertikal Kontur schneiden
- Fräsen
- Ausbohren
- Stanzen
- Schälen
- Formschnitt
- Profilschnitt
- Rollenware
Selbstverständlich stehen wir Ihnen bei Fragen auch persönlich zur Verfügung!
07181 - 999 69 - 0